《企业家日报》(10月9日1版头条)
■任建忠

●华塑股份抢抓机遇精准发力
近期,安徽华塑股份可谓“双喜临门”。在第九届全国化工联合会上,荣获企业管理创新成果二等奖;安徽省氯碱化工工程技术研究中心批准成立。近年来,该公司围绕创新驱动,精细管理,全力打造发展升级版,先后获得国家级高新技术企业认证,取得12项发明专利,17项实用新型专利,完成2项省级科技成果,1个省级自主创新项目,建立省级院士工作站和徐州化工工程设计研究院,科技创新成为公司迈向质量时代“核动力”,今年1-8月份已盈利1.8亿元。
从吃苦头到尝甜头
2013年下半年,华塑股份建设基本完工,从生产调试到正式运行过渡,园区上万台设备,一些装置开开停停,产量低位徘徊,经营亏损严重。特别是该公司乙炔车间发生电石细粉仓爆裂、电石斗提机爆炸,电石自燃着火等事故,该车间就如一个“定时炸弹”,存在随时可能被引爆的危险,70多人的车间,30多人相继离职,一时间人员告急、设备告急、安全告急……
1400多人要吃饭,每天30多万银行利息要偿还,怎么办?时任总经理的丘永桂断然决策,提出:科技创新是华塑走出泥潭的必由之路,必须用技术创新杀出一条血路。
经过调研分析,该公司找到了影响生产最大瓶颈,电石破碎能力满足不了下游生产,原设计两条破碎生产线,采用两级齿辊破碎机。由于电石硬度大,齿辊破碎机故障率高,破碎能力小,无法满足生产需要。加上原设计电石筛分设备采用旋振筛,筛网频繁破损,进出口软连接使用周期短,检修频次高,严重影响生产运行。
该公司拿出“壮士断腕”的决心,新建三条破碎线(两开一备),破碎采用鄂破式破碎机+反击破+环锤式细破,电石筛分采用滚筒筛,使破碎能力由原来的30吨/小时提高到120吨/小时以上。该公司采取电石气体输送工艺,在干法乙炔行业内成为“第一人”,将5mm以下电石粉料采用氮气气力输送,实行密闭循环的方式,将电石物料送至电石料仓,输送氮气经过除尘后返回压缩机入口,实现循环利用。
通过加大乙炔硫酸清净系统改造,降低硫酸消耗,仅此一项每年节省480多万元,经过对破碎、筛分、输送、清净等一系列技术和工艺技改,打破瓶颈,让下游不仅“吃”的饱,而且“吃”的好,该成果被国内乙炔同行称为“干法乙炔的革命”。
集团公司把华塑股份定位为一体两翼,其中一翼,这一翼靠创新展翅,始不垂翅,终能奋翼。3年来华塑股份一举甩掉亏损帽子。从2015年盈利117万元,到2016年盈利2.02亿元,科技创新让公司的“苦果子”,变成了“金果子”。
从0.03吨到3000万元的收获
一度电耗煤多少克、吨PVC耗电石多少吨、用水量减少多少立方,电石废渣如何制石膏,富余蒸汽怎么利用,氢气回收等等,华塑股份精打细算,“抠”消耗指标,主动对标国内先进行业,创新给公司“点亮”增效这盏明灯。
去年以来,该公司把目光聚焦到主产品PVC单耗上,增加2台发生器,控制乙炔水比,抓住包装线跑冒滴漏等问题,吨PVC电石单耗由1.41吨/吨降到1.38吨/吨,每年按照42万吨PVC,可节省近3000万元。由于公司经济体量大,算小帐背后“藏着”大效益,正是跨过吨PVC电石单耗1.38吨/吨这一小步,成就公司发展一大步,迈进氯碱行业第一方阵。
该公司始终抓住技改“法宝”,盯着单耗指标,用创新打好电石炭材的“算盘”珠子,学会“算着干”。电石厂每年生产电石56万吨,消耗炭材40万吨,通过不懈努力,炭材由原来0.77吨/吨降至0.65吨/吨,年节省炭材5.3万吨;消耗石灰57,12万吨,石灰由1.05吨/吨降至0.94吨/吨,年节省石灰5万吨,这让电石厂由“耗能”大户,也变成“节省”大户。
电石厂焦粒、石灰筛下的焦粉、石灰粉,这两种“废渣”,进入电石炉影响炉况,卖掉差价又大,怎么办?公司开展“头脑风暴”,借鉴山西煤粉成球的成熟技术,“嫁接”焦粉和石灰粉成球,经过反复探索,“两球”试验一举成功,既解决了废渣的问题,又节约成本,年节约近3000万元,“两球”的成功运用,成为电石行业的首创,一些电石厂家纷纷“取经”。
加强对废水、废气和固体废弃物的防治,降低单位产品污染物排放强度,大力推进废物资源化利用,提高废水和废气减排的经济环境效益,特别是在乙炔节约用水方面,水资源循环使用率达到90%以上,通过水系统工艺废水回收利用,每小时减少400多吨排放量。制氮机由原来的9台运行,到现在7台运行,每年节省80多万元。公司把创新融入到每个装置、每道工序、每名员工手中,通过2年多探索,实现由量变到质变的飞跃。
从国内领先到行业领跑
建设初期,该公司就把技术创新作为立身之本,提出建设“国内一流,世界领先”循环经济示范园区,立志成为“高耗能行业节能的典范、高污染行业减排的典范”。从大胆采取乙炔气体输送,到废硫酸的处理、用做电石渣制脱硫石膏、电石废渣制水泥、电石等各种粉灰制砖等,园区有27种废渣,利用高达24种,用科技创新把废渣“吃干榨净”。
该公司开展行业对标,先后到新疆天业、内蒙君正、陕西北元、山东信发等国内“老牌”化工企业找标杆,今年以来先后确立187个项目,逐一对标,对标就像一面“镜子”,一直照着公司唯进步,不止步。
用技改扎紧生产“漏洞”。截至5月末,氯碱厂降低触媒消耗,预计年节约218万元。去年,通过乙炔硫酸清净系统改造,将浓硫酸消耗由前期80kg/t-VCM降为25kg/t-VCM,按年产40万吨VCM计算,年节约硫酸约22000吨。硫酸单价按300元/吨计算,年节约660万元,今年公司还荣获安徽省“十二五”节能先进单位。
坚持“两条腿”走路。一方面从外部借力借智,引进各类专业人才170多名,其中包括享受国务院津贴化工专家1人,国内化工学会专家2人等;另一方面充分发挥领军人才作用,每名专家团队带领一个专业技术小组,让技术小组成为“孵化器”。开展攻坚克难英雄榜,选择发电机组整体煤耗下降、降低水泥粉末工序电耗、提高电石冷样发气量等10项技术难题,鼓励技术人员揭榜攻关。各厂发挥QC小组作用,鼓励员工在实际生产中发现问题,其中电石厂石灰窑QC小组被安徽省质量协会评为优秀质量管理小组,机械动力厂QC小组荣获“2017年安徽省优秀QC小组三等奖”。
该公司用科技创新强身健体,领跑氯碱行业,科技创新成为了公司改革发展的“加速器”“助推器”和“核动力”,今天华塑股份就像一列动车组正开足马力全速迈向质量时代。
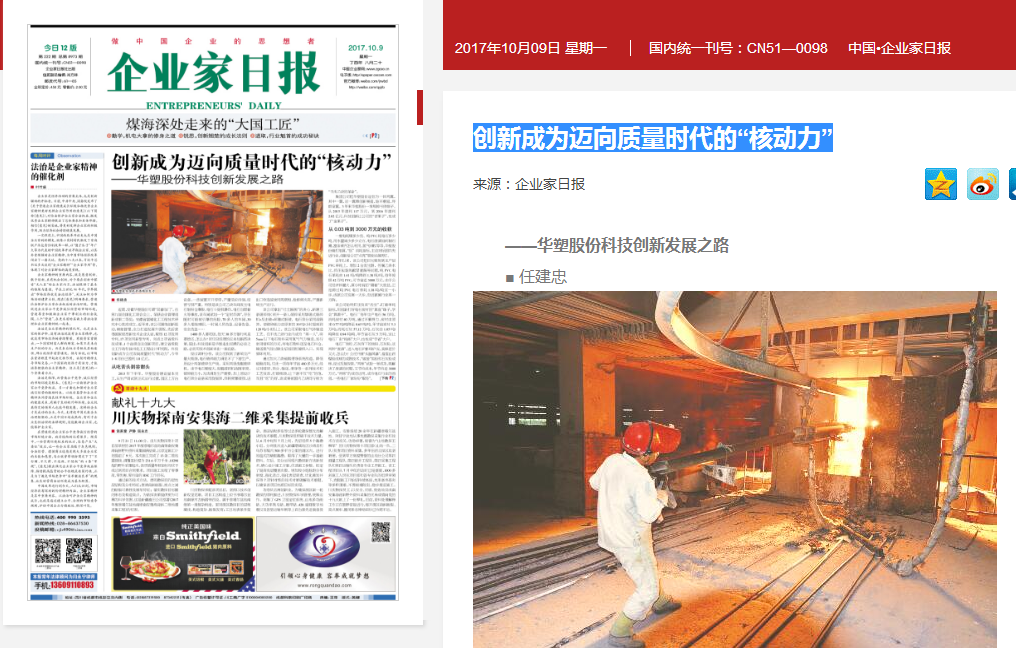